Underwater What!?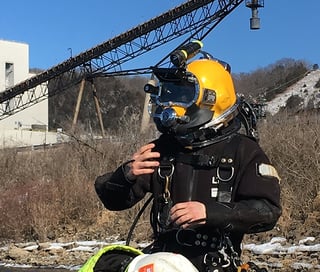
Underwater welding. The two words together sound like a contradictory statement. How could anything involving exposed electricity safely take place under water? At Nelosca, our skilled divers use this method on a variety of structures including dams, bridges and barge terminals. Believe it or not, underwater welding is a very safe and effective method of repair, assuming it is done correctly. There are two ways to perform an underwater weld, using a dry chamber system or wet welding. There are pros and cons to both, but we’re going to focus on wet welding, as this is the majority of what our divers do.
Here’s how it works:
When performing a wet weld, the welder-diver will use a method called Shielded Metal Arc Welding (SMAW), which is also called "stick welding". This method uses three main pieces of equipment, a welding machine, an electrode holder ( also called a stinger), and an electrode. A device called a knife switch is also used, which disconnects the weld circuit to the diver’s stinger, allowing him or her to safely change electrodes.
The diver will instruct the tender at the surface to “make it hot” or “make it cold” as needed. The welding machine must use direct current (DC) electricity for two reasons.
- It decreases the risk of electrocution for the welder-diver
- It provides a more stable arc underwater.
Electricity flows through the consumable electrode and creates an arc of electricity between the electrode and the base material, starting the weld. The electrode is covered with a flux coating which gives off vapors of gas, acting as a shield and leaving behind a layer of slag, which protects the weld from any contamination. The welder-diver always wears rubber gloves to insulate himself or herself from stray electrical current. Care also needs to be taken when positioning the ground so that the diver does not get in the path of the weld circuit, causing potential harm.
So this all makes sense, but how can it be performed underwater?
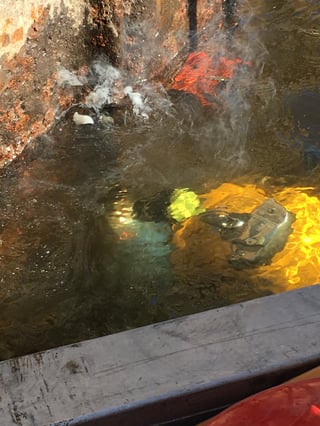
Stick welding creates a gaseous bubble around the welding area that acts as a shield against the surrounding water. It is created when the flux melts around the electrode and is comprised of:
- 70% hydrogen
- 25% carbon dioxide
- 5% carbon monoxide
This bubble protects the weld site from direct exposure to water, however, heat from the electric arc creates thousands of other bubbles that spray up around the welder-diver creating poor visibility. This is especially exacerbated in fresh water environments where the arc is less stable than a salt water environment.
Why weld in the wet?
The primary reason that we weld underwater in wet conditions is it costs significantly less than that of dry chamber welding. It also eliminates the need for expensive cofferdams or other forms of dewatering. Underwater welding is a reliable and versatile repair method for a variety of maritime infrastructure that can be economical and safe when performed correctly.